Picking Armazenagem: Como Melhorar a Eficiência no Estoque
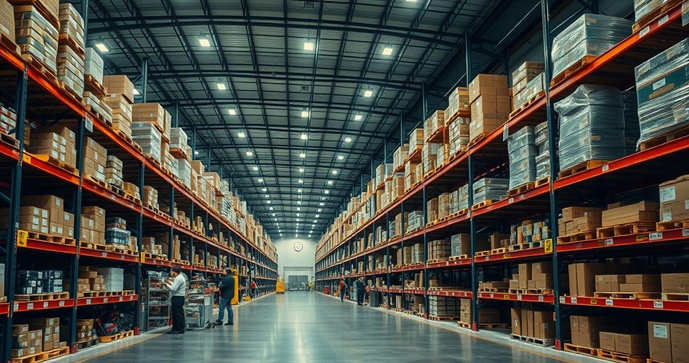
Por: Mayara - 16 de Abril de 2025
Importância do Picking na Gestão de Estoques
A picking armazenagem desempenha um papel fundamental na gestão de estoques, pois afeta diretamente a eficiência operacional e a satisfação do cliente.
Com um sistema de picking bem estruturado, as empresas podem garantir que os produtos certos sejam selecionados e despachados de forma rápida e precisa.
A importância do picking na gestão de estoques é visível em vários aspectos:
- Aumento da Eficiência: Um processo de picking otimizado reduz o tempo gasto na seleção de itens, o que minimiza o tempo de espera para os clientes e acelera o fluxo de trabalho no armazém.
- Redução de Erros: Um sistema de picking bem implementado diminui a margem de erro na seleção de produtos, garantindo que os pedidos sejam atendidos corretamente.
Isso resulta em menos devoluções e maior satisfação do cliente. - Melhor Controle de Inventário: O picking eficaz auxilia no monitoramento preciso dos níveis de estoque, ajudando a evitar excessos ou faltas de produtos.
Com um controle adequado, as empresas podem tomar decisões mais informadas sobre reabastecimento. - Economia de Custos: A eficiência no picking pode levar a uma redução nos custos operacionais, pois otimiza o uso dos recursos humanos e materiais.
Isso se traduz em uma melhor margem de lucro. - Flexibilidade e Escalabilidade: Sistemas de picking ágeis permitem que as empresas se adaptem rapidamente a mudanças na demanda, oferecendo flexibilidade para atender flutuações sazonais ou promoções.
Portanto, ao investir em estratégias e tecnologias de picking, as empresas não apenas melhoram sua operação interna, mas também se posicionam melhor no mercado, oferecendo um serviço de excelência que atende às expectativas dos consumidores.
Tipos de Métodos de Picking e Suas Aplicações
Existem diversos métodos de picking que podem ser utilizados na armazenagem, cada um com suas características e aplicações específicas. A escolha do método adequado depende das necessidades do armazém, do tipo de produtos armazenados e do volume de pedidos. A seguir, apresentamos alguns dos principais tipos de métodos de picking e suas aplicações:
1. Picking por Disposição Aleatória
No picking por disposição aleatória, os itens são armazenados de forma não sequencial, permitindo uma maior utilização do espaço. Este método é ideal para armazéns com um grande número de SKUs (units of stock keeping) e onde a demanda é variada. A flexibilidade é uma das principais vantagens desse método, pois facilita a adaptação a mudanças na demanda.
2. Picking por Zona
O método de picking por zona divide o armazém em áreas específicas, onde cada operador é responsável pela coleta de produtos em uma zona determinada. Isso é eficaz em ambientes de alto volume de pedidos, pois permite a divisão de trabalho e minimiza o tempo de deslocamento dos operadores. Essa técnica é comum em centros de distribuição de grandes varejistas.
3. Picking por Lote
O picking por lote implica na coleta de vários itens ao mesmo tempo, agrupando-os em uma só operação. Este método é vantajoso para armazéns que lidam com itens de alta rotatividade e é frequentemente utilizado em operações que requerem o atendimento a pedidos em grandes quantidades, como no setor alimentar.
4. Picking Direto
No picking direto, os operadores coletam os itens diretamente do armazenamento e os preparam para envio. Esse método é simples e eficiente, adequado para armazéns menores ou para produtos de alta demanda, onde os itens estão facilmente acessíveis.
5. Picking Assistido por Tecnologia
O picking assistido por tecnologia utiliza ferramentas como leitores de código de barras ou sistemas automatizados de coleta para aumentar a precisão e a eficiência. Esta abordagem é ideal para armazéns modernos que buscam maximizar a produtividade e minimizar erros.
Cada um desses métodos de picking tem suas vantagens e desvantagens, e a escolha ideal dependerá das especificidades das operações de cada empresa. Implementar o método correto pode resultar em melhorias significativas na eficiência do armazém e na satisfação do cliente.
Tecnologia e Ferramentas para Picking Armazenagem
A adoção de tecnologia e ferramentas adequadas é essencial para otimizar os processos de picking armazenagem. Com a evolução das tecnologias no setor logístico, diversas soluções se tornaram disponíveis para melhorar a eficiência, a precisão e a agilidade nas operações de separação de produtos. Aqui estão algumas das principais tecnologias e ferramentas utilizadas no picking armazenagem:
1. Sistemas de Gerenciamento de Armazém (WMS)
Os sistemas de gerenciamento de armazém (WMS) são softwares projetados para otimizar as operações de armazém, incluindo o processo de picking. Eles permitem o rastreamento em tempo real do inventário, facilitando a organização e a localização dos produtos. A utilização de WMS pode melhorar significativamente a eficiência do picking, já que os operadores recebem orientações claras sobre onde encontrar os itens necessários.
2. Dispositivos Móveis e Sistemas de Coleta
A utilização de dispositivos móveis, como tablets e smartphones, equipados com aplicativos de picking, permite que os operadores realizem a coleta de itens de forma mais ágil. Esses sistemas geralmente incluem recursos de leitura de código de barras e verificação de itens, o que ajuda a reduzir erros e aumentar a eficiência.
3. Leitores de Código de Barras e RFID
Os leitores de código de barras são ferramentas fundamentais no processo de picking, pois permitem a identificação rápida e precisa dos produtos. O uso de RFID (identificação por radiofrequência) também está em ascensão, pois fornece uma forma ainda mais eficiente de rastreamento dos itens em tempo real, facilitando a gestão do estoque e a acuracidade na separação.
4. Equipamentos de Automação
Os sistemas automatizados, como transportadores, robôs de picking e estantes automatizadas, têm sido cada vez mais utilizados para agilizar o processo de separação. Esses dispositivos podem atuar de maneira precisa e rápida, minimizando o tempo de manuseio e aumentando a produtividade.
5. Análise de Dados e Business Intelligence
A análise de dados desempenha um papel fundamental na otimização do processo de picking. Ferramentas de Business Intelligence (BI) permitem que as empresas analisem o desempenho operacional, identifiquem gargalos e tomem decisões baseadas em dados para aprimorar constantemente suas operações de armazém.
6. Integração com E-commerce
Para empresas que operam no e-commerce, a integração de sistemas de picking com plataformas de vendas online é crucial. Isso garante que os pedidos sejam processados e enviados de forma rápida e eficiente, melhorando a experiência do cliente e aumentando a taxa de satisfação.
Investir em tecnologia e ferramentas para picking armazenagem não apenas melhora a eficiência operacional, mas também contribui para a sustentabilidade da empresa a longo prazo. A adoção de soluções inovadoras é uma estratégia vencedora para se destacar em um mercado cada vez mais competitivo.
Desafios Comuns na Implementação do Picking
A implementação de um sistema de picking eficiente é uma tarefa complexa e pode enfrentar diversos desafios. Esses obstáculos podem afetar a eficiência operacional e a satisfação do cliente. Identificar esses desafios antecipadamente pode ajudar na formulação de estratégias para superá-los.
A seguir, estão alguns dos desafios comuns enfrentados na implementação do picking:
1. Falta de Planejamento
Um planejamento inadequado pode levar à implementação de um sistema de picking ineficiente. Antes de iniciar, é essencial realizar uma análise detalhada das operações, incluindo a identificação do volume de pedidos, o tipo de produtos e a disposição do armazém. Sem um planejamento cuidadoso, as empresas podem enfrentar dificuldades no fluxo de trabalho e na alocação de recursos.
2. Resistência à Mudança
A mudança para um novo sistema de picking pode encontrar resistência por parte da equipe. Funcionários acostumados a métodos tradicionais podem hesitar em adotar novas tecnologias ou métodos de trabalho. Para contornar esse desafio, é fundamental fornecer treinamento adequado e mostrar os benefícios que a nova abordagem trará tanto para a empresa quanto para os colaboradores.
3. Integração de Sistemas
A integração de diferentes sistemas de gerenciamento pode ser um desafio significativo. Problemas de compatibilidade entre softwares existentes e novos sistemas de picking podem resultar em falhas na comunicação e no compartilhamento de dados. Escolher plataformas que ofereçam compatibilidade ou garantir a implementação de interfaces de integração é crucial para evitar esses problemas.
4. Gestão de Inventário Ineficiente
Uma gestão de inventário ineficiente pode impactar diretamente o desempenho do picking. A falta de precisão nos registros de estoque pode levar a erros na separação de produtos, atrasos e insatisfação do cliente. Portanto, implementar soluções de monitoramento em tempo real e utilizar tecnologias como RFID e WMS é essencial para garantir controle adequado do inventário.
5. Ergonomia e Segurança do Trabalho
A ergonomia e a segurança dos funcionários são aspectos importantes que muitas vezes são negligenciados durante a implementação de um sistema de picking. Segurança inadequada pode aumentar o risco de acidentes, enquanto a falta de ergonomia pode levar a problemas de saúde a longo prazo para os colaboradores. Medidas devem ser adotadas para garantir que o ambiente de trabalho seja seguro e confortável, como o uso de equipamentos ergonômicos.
6. Custos Iniciais Elevados
Os custos iniciais associados à implementação de um sistema de picking eficiente, incluindo treinamento, aquisição de tecnologia e reestruturação do armazém, podem ser um desafio. Muitas empresas hesitam em fazer esses investimentos, mas é importante enxergar isso como um investimento que trará retorno a longo prazo, melhorando a eficiência e reduzindo custos operacionais.
Superar esses desafios requer um compromisso com a melhoria contínua e uma disposição para adaptar e ajustar estratégias conforme necessário. Com o suporte adequado e um planejamento cuidadoso, as empresas podem implementar sistemas de picking que atendam às suas necessidades e melhorem significativamente suas operações.
As Melhores Práticas para a Picking Armazenagem
Adotar as melhores práticas para a picking armazenagem é essencial para otimizar a eficiência e a eficácia do processo de separação de produtos. A seguir, elencamos algumas das principais práticas que podem ser implementadas para garantir um sistema de picking mais eficaz e produtivo:
1. Classificação dos Produtos
Uma das melhores práticas é classificar os produtos com base em sua rotatividade e demanda. Implementar um sistema ABC, onde os produtos são classificados em categorias A (alto valor e alta rotatividade), B (valor e rotatividade média) e C (baixo valor e baixa rotatividade), pode ajudar a otimizar a disposição dos itens no armazém. Produtos de alta demanda devem ser armazenados mais próximos da área de envio, reduzindo o tempo de picking.
2. Layout Eficiente do Armazém
O layout do armazém deve ser planejado para maximizar a eficiência do picking. Isso inclui a disposição adequada de corredores, estantes e áreas de espera. Um layout bem planejado reduz o tempo de deslocamento dos operadores e facilita a localização dos produtos, aumentando a eficiência geral.
3. Utilização de Tecnologia
A adoção de tecnologias avançadas, como sistemas de gerenciamento de armazém (WMS) e dispositivos móveis para coleta, pode melhorar significativamente o processo de picking. Essas ferramentas ajudam a automatizar tarefas, reduzir erros e fornecer informações em tempo real, garantindo que as operações sejam realizadas de forma mais eficiente.
4. Treinamento da Equipe
Investir no treinamento da equipe é fundamental para o sucesso de um sistema de picking. Operadores bem treinados entendem os processos e as ferramentas que utilizam, o que contribui para uma operação mais eficiente e reduz o número de erros. Além disso, a capacitação contínua ajuda a equipe a se adaptar a novas tecnologias e métodos.
5. Monitoramento e Avaliação Contínua
Implementar um sistema de monitoramento de desempenho pode fornecer dados valiosos sobre a eficiência do processo de picking. Avaliar métricas como tempo de ciclo, volume de pedidos atendidos e erro de separação ajuda a identificar áreas de melhoria. Avaliações regulares permitem ajustes contínuos que podem melhorar o desempenho ao longo do tempo.
6. Promoção de um Ambiente de Trabalho Seguro e Ergonômico
Criar um ambiente de trabalho que priorize a segurança e a ergonomia é essencial. Equipamentos ergonômicos, como carrinhos de transporte e prateleiras ajustáveis, devem ser utilizados para minimizar o risco de lesões e aumentar a produtividade dos colaboradores. Uma abordagem proativa em relação à segurança do trabalho deve ser constantemente promovida.
7. Melhoria no Processo de Picking
Por fim, sempre busque formas de otimizar o processo de picking, como a implementação de métodos de picking por zoneamento ou picking assistido por tecnologia. A adoção de novas abordagens que aumentem a eficiência e reduzam erros é vital para um sistema de picking eficaz.
Implementar essas melhores práticas para a picking armazenagem pode reduzir custos, aumentar a eficiência e melhorar a satisfação do cliente, criando um armazém mais eficaz e competitivo no mercado.
Como Medir a Eficiência do Picking em Seu Armazém
Medir a eficiência do picking em um armazém é crucial para identificar áreas de melhoria e garantir operações otimizadas. Existem diversas métricas e métodos que podem ser utilizados para avaliar o desempenho do processo de picking. A seguir, apresentamos algumas abordagens eficazes para medir a eficiência do picking:
1. Tempo de Ciclo de Picking
O tempo de ciclo de picking refere-se ao tempo total que um operador leva para completar uma tarefa de picking, desde o início até a conclusão do pedido. Reduzir o tempo de ciclo é uma indicação clara de aumento de eficiência. Para calcular essa métrica, registre o início e o fim de cada operação e faça a média dos tempos registrados ao longo de um período específico.
2. Taxa de Exatidão
A taxa de exatidão determina a precisão do processo de picking, ou seja, a porcentagem de pedidos que foram enviados corretamente e sem erros. Uma alta taxa de exatidão é fundamental para manter a satisfação do cliente. Para calcular, divida o número de pedidos corretos pelo total de pedidos processados e multiplique por 100.
3. Volume de Pedidos Atendidos
A métrica de volume de pedidos atendidos avalia quantos pedidos são processados em um determinado período. Essa métrica pode ser monitorada diariamente, semanalmente ou mensalmente, e ajuda a entender a capacidade de trabalho do armazém. Um aumento no volume de pedidos atendidos geralmente indica melhorias na eficiência do sistema de picking.
4. Utilização de Espaço
A eficiência do picking também pode ser medida pela utilização do espaço no armazém. Um melhor aproveitamento do espaço pode facilitar o acesso aos produtos e reduzir o tempo de deslocamento. A utilização do espaço pode ser avaliada monitorando a densidade de armazenamento e ajustando os layouts de acordo com a rotatividade dos itens.
5. Custo por Pedido
O custo por pedido é uma métrica importante para avaliar a eficiência econômica do processo de picking. Ele considera todos os custos associados ao processo de separação e envio de um pedido. Para calcular, some todos os custos operacionais do armazém e divida pelo número total de pedidos atendidos em um determinado período.
6. Feedback da Equipe
Além de métricas quantitativas, o feedback da equipe envolvida no processo de picking é uma fonte valiosa de informações. Realizar reuniões periódicas e colher opiniões dos operadores pode fornecer insights sobre dificuldades enfrentadas, possíveis melhorias e sugestões que podem não ser capturadas em dados quantitativos.
7. Análise de Dados e Relatórios
Utilizar ferramentas de análise de dados para compilar e visualizar métricas de desempenho pode ajudar a identificar tendências e áreas que precisam de atenção. Relatórios regulares permitem uma análise detalhada do desempenho do picking e são essenciais para a tomada de decisões informadas.
Implementar essas abordagens de medição da eficiência do picking ajudará a criar um ambiente mais produtivo e a melhorar continuamente as operações do armazém. Avaliações regulares não apenas revelam o desempenho atual, mas também ajudam a criar um plano de ação para melhorias futuras.
A gestão eficiente do picking armazenagem é fundamental para o sucesso de qualquer operação logística. Ao adotar as melhores práticas e investir em tecnologia, as empresas podem não apenas otimizar seus processos, mas também aumentar a satisfação do cliente e reduzir custos operacionais.
Identificar e superar os desafios comuns na implementação do picking é essencial para garantir resultados positivos a longo prazo. Além disso, medir a eficiência do processo por meio de métricas específicas permite que as empresas ajustem suas operações continuamente, buscando melhorias constantes.
Com uma estratégia sólida e o comprometimento em aprimorar continuamente o sistema de picking, as organizações podem garantir uma vantagem competitiva no mercado, proporcionando um serviço de excelência aos seus consumidores.